Maximizing Efficiency and Quality with Rapid Prototype Molding
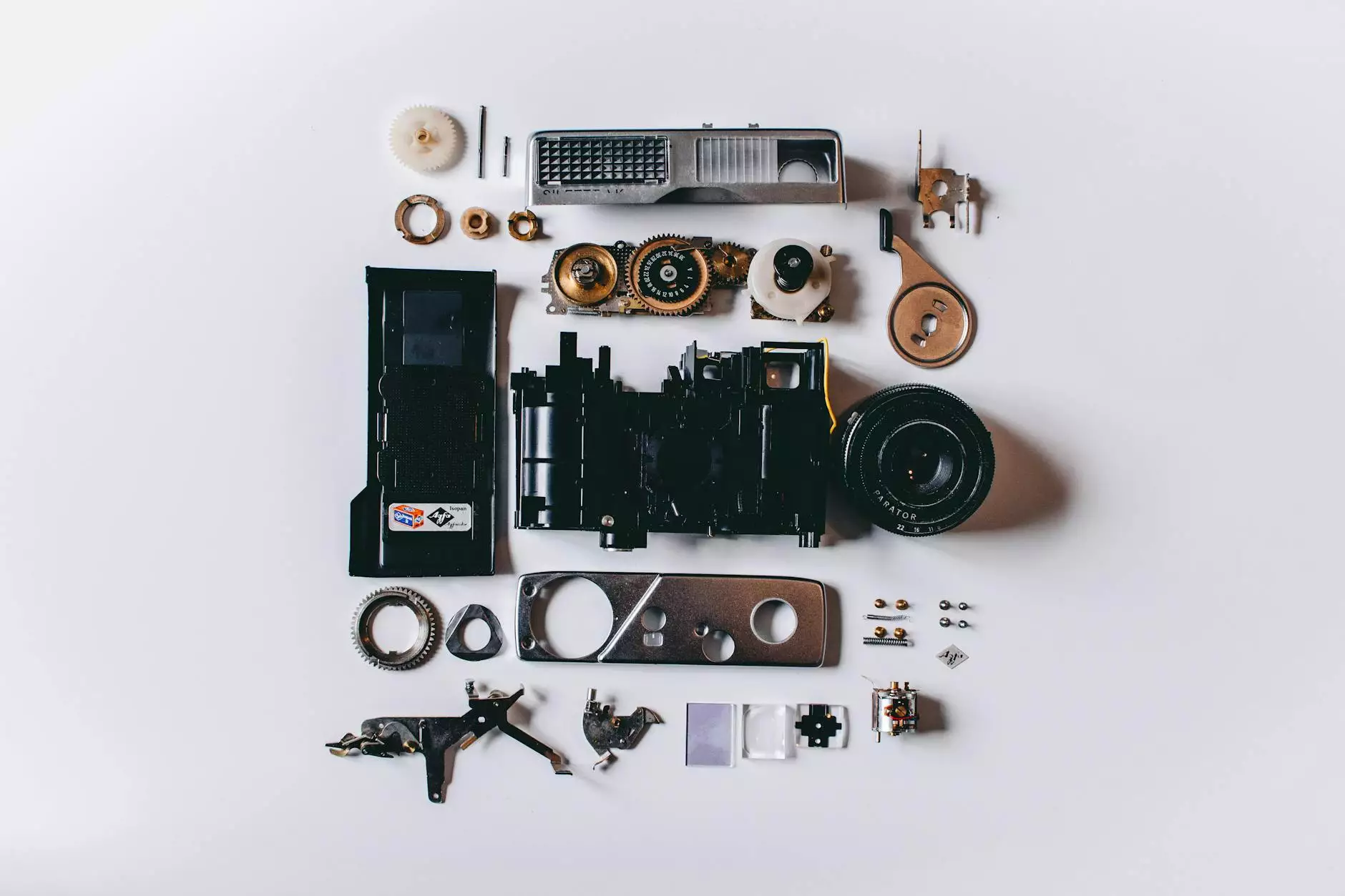
In today's fast-paced business environment, the demand for rapid product development and manufacturing is ever-increasing. Companies are constantly searching for innovative ways to meet customer demands swiftly while maintaining the highest quality. One such innovation that has gained immense popularity is rapid prototype molding. This technique revolutionizes the way metal fabricators operate, enabling them to enhance productivity, reduce costs, and significantly shorten lead times.
What is Rapid Prototype Molding?
Rapid prototype molding is a manufacturing process that allows for the quick production of prototypes using advanced techniques such as 3D printing, CNC machining, and injection molding. This method is crucial for product development as it enables businesses to create functional prototypes in a fraction of the time compared to traditional methods. With this technology, metal fabricators can test their designs, iterate on them quickly, and bring products to market faster than ever before.
The Importance of Rapid Prototype Molding in Metal Fabrication
Metal fabrication is a critical component of numerous industries, including automotive, aerospace, electronics, and construction. The integration of rapid prototype molding in metal fabrication plays a significant role in enhancing the overall efficiency of operations. Here are several reasons why this process is essential:
- Accelerated Product Development: Rapid prototyping significantly reduces the time needed to develop products, allowing for faster market entry and the ability to meet customer needs promptly.
- Reduced Costs: By identifying design flaws early in the development process, businesses can avoid costly revisions and minimize waste.
- Improved Collaboration: Enhanced visualization of prototypes enables better communication between teams, stakeholders, and clients, resulting in a more streamlined product development process.
- Customization: Rapid prototype molding allows for easy modifications and customizations, catering to specific client needs and preferences.
How Rapid Prototype Molding Works
The process of rapid prototype molding can be broken down into several key stages:
1. Design Generation
The first step involves creating a digital 3D model of the product using Computer-Aided Design (CAD) software. This model serves as the foundation for the entire prototyping process.
2. Prototyping
Depending on the complexity and requirements of the design, various prototyping techniques can be employed. Common methods include:
- 3D Printing: Ideal for creating complex geometries and fast prototyping.
- CNC Machining: Provides high precision and is perfect for metal components.
- Injection Molding: Suitable for producing larger quantities of prototypes with consistent quality.
3. Testing and Evaluation
Once the prototype is produced, it undergoes rigorous testing to evaluate its performance, functionality, and adherence to specifications. Feedback from this stage is crucial for making necessary adjustments.
4. Final Production
After refining the design based on testing results, businesses can proceed to full-scale production, confident in the quality and functionality of their product.
Advantages of Utilizing Rapid Prototype Molding
The advantages of incorporating rapid prototype molding into a business's operational workflow are manifold:
- Enhanced Innovation: The speed and flexibility of rapid prototyping allow businesses to experiment with new ideas and designs, spurring innovation.
- Market Responsiveness: Companies can quickly pivot and adapt to changing market demands by rapidly developing and refining prototypes.
- Quality Control: The iterative process of prototyping helps maintain high standards in product quality as designs are tested and improved continuously.
- Competitive Advantage: Businesses that implement rapid prototyping effectively can outperform competitors who rely on traditional methods.
Challenges in Rapid Prototype Molding
While rapid prototype molding offers numerous benefits, it is not without its challenges:
- Material Limitations: Some materials may not be suited for rapid prototyping, which can restrict design options.
- Technical Expertise: Businesses may require skilled personnel to manage sophisticated prototyping technologies effectively.
- Initial Investment: The costs associated with advanced prototyping equipment and technology can be a barrier for some companies.
Future Trends in Rapid Prototype Molding
The landscape of rapid prototype molding is constantly evolving, driven by technological advancements and changing market needs. Here are some key trends to watch:
1. Advanced Materials
The development of new materials is enhancing the capabilities of rapid prototyping. Innovations like high-strength polymers, biocompatible materials, and metal alloys are expanding the range of applications for prototypes.
2. Integration with AI and Automation
Artificial Intelligence (AI) and automation are poised to revolutionize rapid prototyping, improving design optimization, and streamlining the production process.
3. Sustainable Practices
As industries strive for sustainability, eco-friendly materials and processes in rapid prototyping are gaining traction. Companies will increasingly prioritize reducing waste and energy consumption in their production methods.
Why Choose DeepMould.net for Your Rapid Prototype Molding Needs?
When it comes to adopting rapid prototype molding for your business, selecting the right partner is crucial. At DeepMould.net, we pride ourselves on our expertise in metal fabrication and prototyping services. Here’s why we stand out:
- Experience: With years of experience in the industry, we understand the intricacies of rapid prototype molding and the needs of our clients.
- State-of-the-Art Technology: We leverage the latest technologies to deliver high-quality prototypes efficiently and accurately.
- Customization: Our team works closely with clients to provide tailored solutions that meet unique business requirements.
- Commitment to Quality: We adhere to stringent quality control processes to ensure that every prototype meets industry standards.
Conclusion
The integration of rapid prototype molding into metal fabrication is a game-changer for businesses looking to innovate and thrive in a competitive landscape. By streamlining the product development process, reducing costs, and improving quality, this technique empowers companies to meet the demands of modern markets effectively. Choosing a reliable partner like DeepMould.net can further enhance these benefits, ensuring your business stays at the forefront of innovation.
Embrace the future of manufacturing with rapid prototype molding and unlock the potential for unprecedented growth and success!