Unlocking the Potential of Injection Plastic Molding
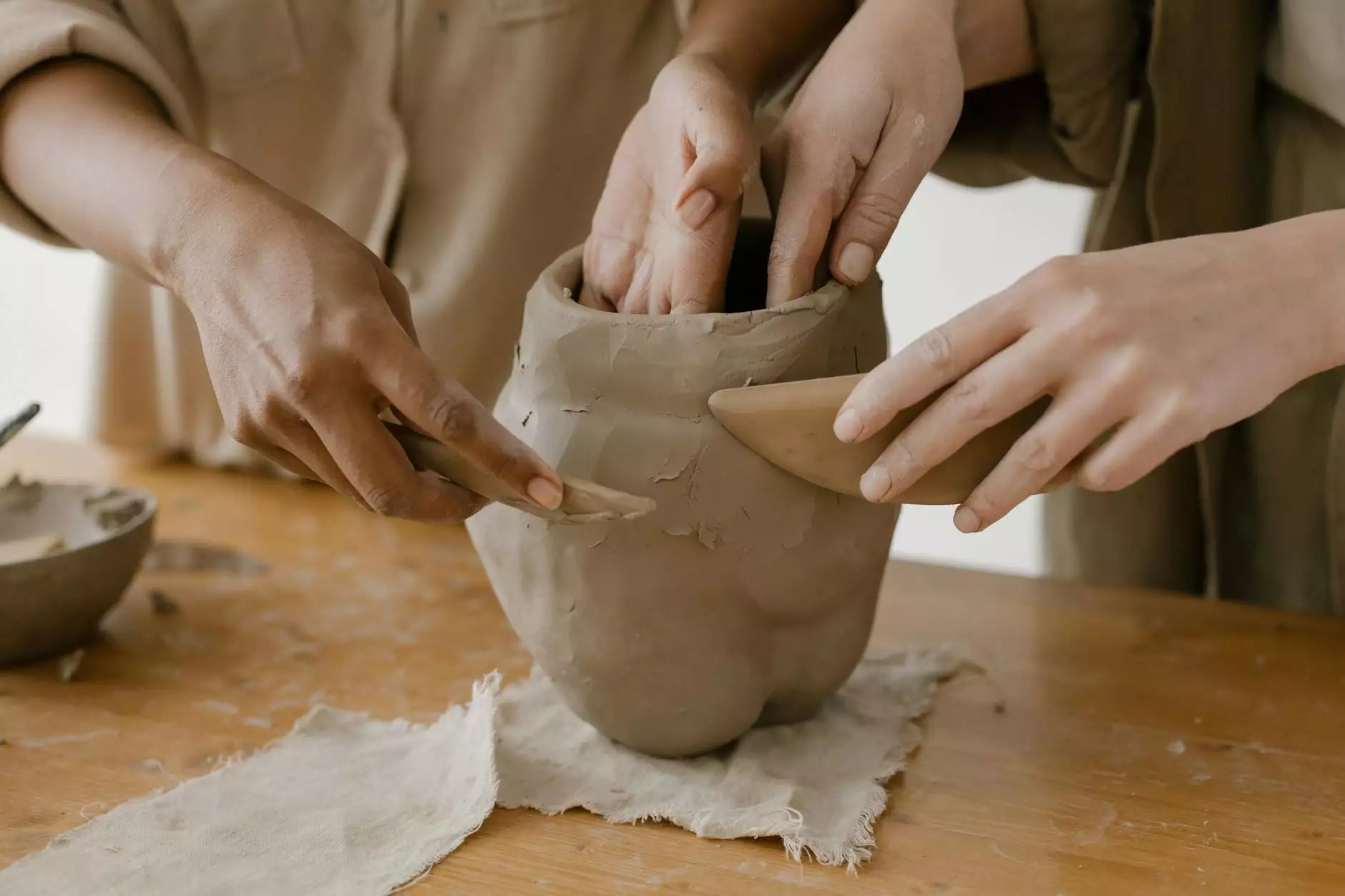
In today's fast-paced manufacturing world, the need for efficiency and effectiveness is paramount. One of the most innovative techniques that has emerged to meet these demands is injection plastic molding. This article delves into the world of injection plastic molding, exploring its benefits, applications, and how it can drive business growth, particularly in the sector of metal fabricators.
What is Injection Plastic Molding?
Injection plastic molding is a manufacturing process used to create parts by injecting molten plastic into a mold. This method enables the production of complex shapes with high precision and repeatability. The process starts with melting plastic pellets, which are then injected into a mold cavity under high pressure. Once the plastic cools and solidifies, the mold opens, and the finished part can be easily ejected.
Key Components of the Injection Molding Process
- Molding Machine: The machine that performs the injection process, which can vary in size and capacity based on production needs.
- Mold: A hollow metallic block designed to create the shape of the plastic part. Molds can be single or multi-cavity.
- Plastic Material: Various thermoplastic and thermosetting polymers are used depending on the product requirements.
- Injection Unit: The component of the machine that melts and injects the plastic.
- Clamping Unit: Holds the mold in place during injection and cooling.
The Advantages of Injection Plastic Molding
Injection plastic molding offers numerous advantages for manufacturers, especially those involved in metal fabrication. Below are some of the key benefits:
1. High Efficiency and Speed
One of the most significant advantages of injection plastic molding is its capability for high-volume production. Once the mold is designed and created, thousands of identical parts can be produced quickly, significantly reducing time-to-market.
2. Precision and Consistency
The nature of the molding process allows for the creation of parts with tight tolerances and uniformity. This is particularly vital in industries where precision components are required, such as in automotive and aerospace applications.
3. Material Versatility
With an array of plastic materials available, companies can choose the best type for their application. Common materials include:
- ABS (Acrylonitrile Butadiene Styrene): Known for its toughness and impact resistance.
- Polycarbonate: Offers high strength and durability.
- PP (Polypropylene): Lightweight and resistant to many chemicals.
4. Cost-Effective Production
Although the initial costs associated with mold creation can be high, the long-term savings on production costs are significant. High volume yields lower costs per unit, making injection molding a cost-effective choice for large manufacturing runs.
Applications of Injection Plastic Molding in Metal Fabrication
Metal fabricators can leverage injection plastic molding to enhance their product offerings, improve efficiencies, and broaden their market reach. Below are some noteworthy applications:
1. Manufacturing Precision Components
In industries such as automotive, electronics, and aerospace, the demand for precision parts is ever-increasing. Injection molding provides an avenue for fabricators to produce intricate designs that meet specific fit and performance criteria.
2. Creating Custom Metal Parts
Custom metal parts can benefit from injection molded plastic components that serve as housings or enclosures. This allows for a combination of materials that leverage the advantages of both metals and plastics.
3. Integration with Metal Components
Injection molding can be used to manufacture parts that integrate seamlessly with metal components. For example, injection-molded plastic components are often used in electronic devices that require insulated enclosures to protect sensitive electronic parts.
Environmental Considerations
As sustainability becomes a critical focus for businesses, injection plastic molding is evolving to meet these needs. Manufacturers are now increasingly using biodegradable plastics and implementing recycling programs to reduce waste.
1. Eco-Friendly Materials
Innovations in polymer science are leading to the development of eco-friendly materials that can be used for injection molding. These materials provide sustainable alternatives while maintaining performance and durability.
2. Energy Efficient Practices
Modern injection molding machines are designed to be energy efficient, further reducing the environmental impact. Streamlined processes and the use of energy-saving technologies contribute to a greener manufacturing environment.
Challenges in Injection Plastic Molding
Despite its numerous advantages, businesses must be aware of the challenges posed by injection plastic molding:
1. High Initial Costs
The creation of high-quality molds necessitates a significant initial investment. However, this cost is often offset by the long-term efficiency and lower production costs associated with high-volume manufacturing.
2. Design Limitations
While injection molding allows for complex shapes, there are constraints related to mold design, such as draft angles and undercuts. A skilled designer can overcome these limitations, but upfront planning is essential.
3. Maintenance of Equipment
Regular maintenance of injection molding machines is required to ensure optimal performance and prevent downtime. A robust maintenance schedule can help mitigate these challenges.
Conclusion
In conclusion, injection plastic molding stands as a transformative manufacturing process, particularly beneficial for metal fabricators. By harnessing the speed, efficiency, and versatility of injection molding, businesses can elevate their production capabilities, offering high-quality products that meet the demands of today’s market. The integration of sustainable practices and innovative materials further enhances the appeal of this method, enabling companies to align with environmental goals while fulfilling customer needs.
For those looking to explore the potential of injection plastic molding, partnering with experts in the field, such as those at Deep Mould, can be an invaluable step toward successful implementation and growth.