Boosting Business Success with Ceramic Injection Molding
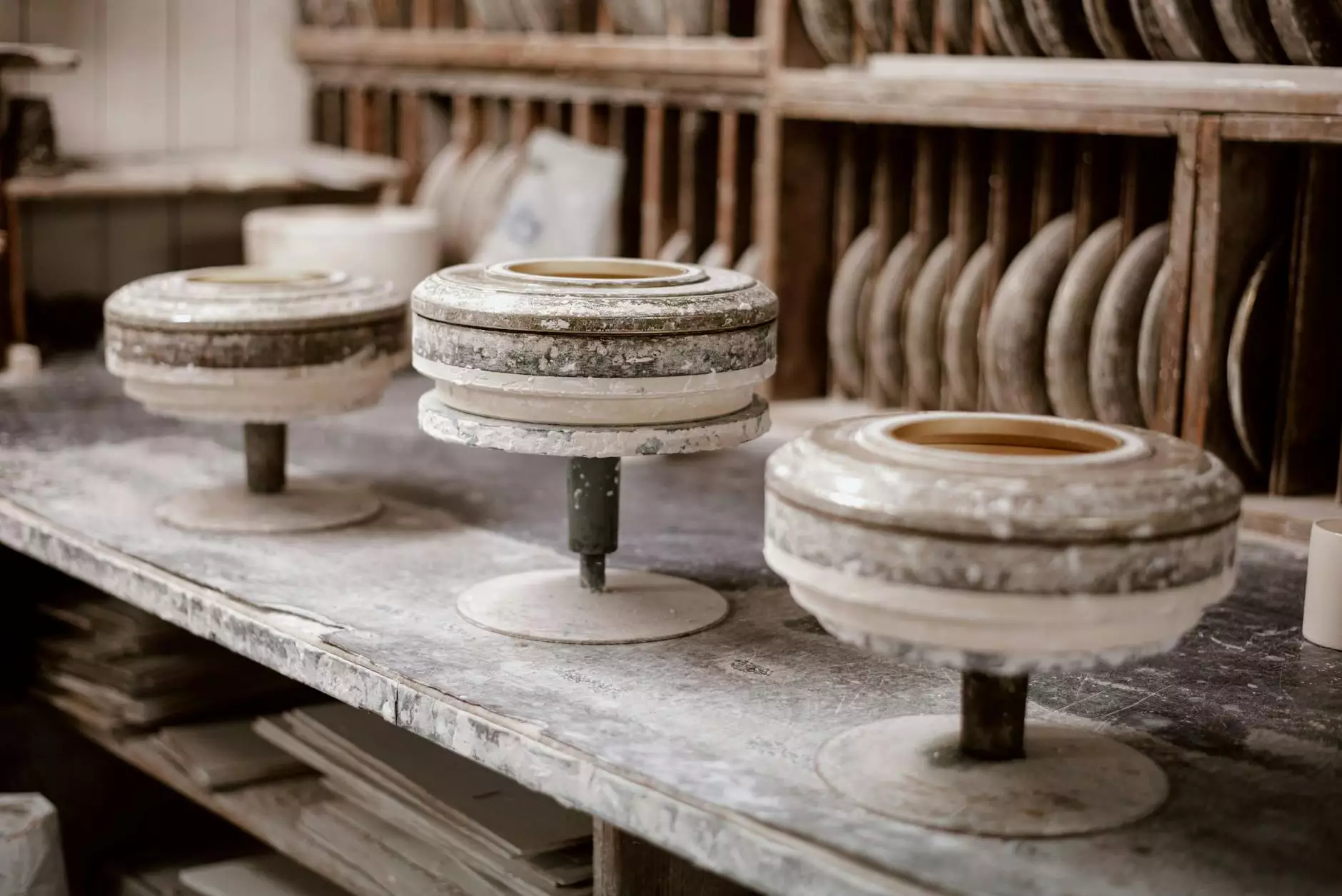
Introduction
In the fast-paced world of electronics manufacturing, staying ahead of the competition is crucial. Businesses need to constantly explore cutting-edge technologies and advancements to improve their processes, enhance product quality, and drive growth. One such technology that has revolutionized the industry is ceramic injection molding (CIM). In this article, we will delve into the exciting world of CIM and how it can contribute to the success of your business.
The Power of Ceramic Injection Molding
Ceramic injection molding combines the benefits of ceramic materials with the flexibility and efficiency of injection molding. This process allows for the manufacturing of complex ceramic components with high precision and consistency. Electronics businesses can leverage CIM to create intricate geometries that were previously unattainable with traditional ceramic manufacturing methods.
Unparalleled Precision and Consistency
Ceramic injection molding enables businesses to achieve unparalleled precision and consistency in the manufacturing of ceramic components. The ability to mold intricate shapes with tight tolerances ensures that every product meets the required specifications. This level of precision is especially critical in the electronics industry, where even the smallest deviation can affect the performance and reliability of the final product.
Improved Design Flexibility
With CIM, businesses can overcome the limitations of traditional ceramic manufacturing processes. The moldability of ceramic materials allows for the production of complex shapes, including thin walls, fine features, and 3D geometries. This opens up new design possibilities, enabling engineers to optimize their designs for functionality, space-saving, and aesthetics.
Enhanced Material Performance
Ceramic materials offer a wide range of desirable properties, including high thermal conductivity, excellent wear resistance, and superior electrical insulation. By utilizing CIM, businesses can fully harness these material properties, enhancing the performance and reliability of their electronic products. The ability to tailor ceramic compositions and adjust material characteristics further expands the applications and benefits of CIM.
Streamlined Manufacturing Process
CIM offers significant advantages in terms of manufacturing efficiency. The injection molding process allows for high-volume production with minimal material waste. This results in cost savings and shorter lead times, giving businesses a competitive edge in meeting tight market demands. Additionally, CIM eliminates the need for extensive machining and manual labor, reducing labor costs and potential human errors.
Applications of Ceramic Injection Molding in Electronics
The versatility of CIM makes it an ideal choice for numerous applications within the electronics industry. Some key areas where ceramic injection molding excels include:
Microelectronics
CIM plays a vital role in the production of microelectronic components such as packages, substrates, and connectors. These microelectronics require high precision, excellent thermal management, and reliable electrical insulation, all of which CIM can deliver. The ability to integrate multiple functionalities into a single component further enhances the performance and miniaturization of electronic devices.
Sensor Technology
Sensors are the backbone of modern electronics, enabling devices to interact with their environment. CIM enables the production of intricate sensor components with fine details and high sensitivity. The excellent dielectric properties of ceramics provide sensors with enhanced performance in terms of signal processing, accuracy, and reliability.
Power Electronics
CIM is widely used in the manufacturing of power electronics components such as capacitors, resistors, and insulators. Ceramic materials offer exceptional thermal conductivity, allowing these components to effectively dissipate heat. This thermal management capability is crucial for power electronics, ensuring optimal performance and long-term reliability.
Medical Devices
CIM finds extensive application in the medical device industry, where biocompatible materials and precision are paramount. The ability to produce intricate shapes and custom geometries provides opportunities for innovative medical devices that are safe, reliable, and cost-effective.
Choosing Nolato for Your Ceramic Injection Molding Needs
When it comes to ceramic injection molding for your electronics business, partnering with an experienced and reliable manufacturer is crucial. Nolato Electronics, a leader in the industry, offers comprehensive CIM solutions tailored to meet your specific requirements.
With state-of-the-art facilities and a team of skilled engineers, Nolato Electronics combines advanced CIM technology with a commitment to delivering superior quality products. From concept to production, Nolato works closely with businesses to ensure seamless integration of ceramic components into their electronics, guaranteeing the highest level of performance and customer satisfaction.
Conclusion
The transformative power of ceramic injection molding cannot be overstated. This advanced technology has the potential to revolutionize the way electronics businesses design and manufacture their products. By harnessing the precision, flexibility, and material properties of CIM, businesses can unlock new opportunities, enhance product performance, and gain a competitive edge. Partnering with Nolato Electronics ensures that your ceramic injection molding needs are met with expertise and innovation. Embrace the future of electronics manufacturing with CIM and drive your business towards sustainable success.